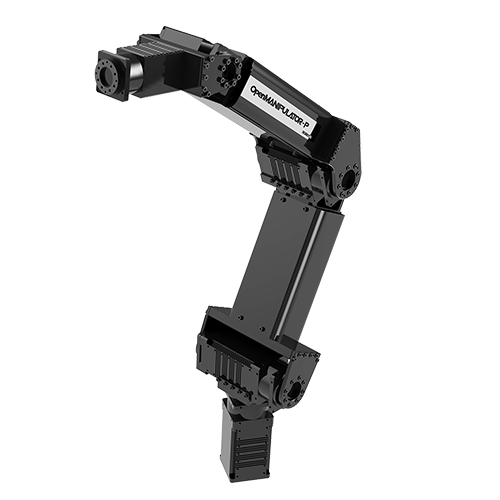
.
Product Name : OpenMANIPULATOR-P
Model Name : RM-P60-RNH
User Programmable Open-Source Manipulator System
Modular Platform for Easy Maintenance and Customization
No External Control Box & High Weight-to-Payload Ratio
OpenMANIPULATOR-P | 1 (Fully-assembled) |
---|---|
Hard Case | 1 |
U2D2 | 1 |
Spare Cables (4P, 2P) | 1 |
Screw Sets (WB M3x8 etc) | 1 |
4P Expansion Hub | 1 |
DOF | 6 |
---|---|
Payload (kg) | 3 |
Repeatability (mm) | ±0.05 |
Speed (Each joint, deg/sec) | 180 |
Weight (kg) | 5.5 |
Reach (mm) | 645 |
Rated Voltage (VDC) | 24 |
Communication | RS-485 (Multi Drop Bus) |
Motor Output / Joint |
200W / 2ea 100W / 2ea 20W / 2ea |
Software | ROS (Ubuntu Linux) |
Controller |
PC (Not Included) |
ROBOTIS Manipulator controller package based on integrated software
OpenMANIPULATOR-P Library (Kinematics,Trajectory and Dynamixel Controller).
GUI program package for setting and monitoring control parameters.
MoveIt! package for OpenMANIPULATOR-P
Simulation package based on Gazebo Simulator
Teleoperation examples of keyboard and Joystick
Research and Education
Kinematics and Dynamics Experiment
Research and Design a Dual Arm Robot
Build a Mobile Robot System
Industrial Operation
Inspection Equipment
Small-Scale Delivery System
Power supply and PC are not included.
Please purchase separately according to your usage environment.
ID | 1 |
---|---|
Baud Rate | 57600 bps |
All-in-one Modular Design
DC Motor + Controller + Driver + Sensor + Cycloid Reduction Gear
Compact and Lightweight
Minimized module size with compact and lightweight cycloid reduction gear.
High weight-to-output ratio(0.05Nm/g)
High impact resistance ( over 400%)
High Precision and Low Backlash
Contactless (Magnetic) Absolute Encoder(by AMS) & Incremental Encoder for Precise Positioning
Low backlash (3~4arcmin)
Performance data provided tested by Korea Laboratory Accreditation Scheme(KOLAS)
Current-Based Torque Control
High speed current sensing algorithm and current feedback control
Triple-loop control for current, speed and position feedback.
User Friendly development environment
Provide C language based library
Various solution examples (C++, LabVIEW, C#, eclipse, JAVA, etc..)